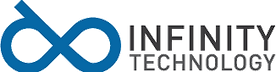
Bespoke Just In Time / Just In Sequence System
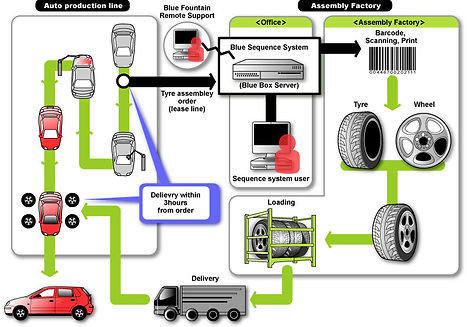
Benefits of JIS
-
Increases suppliers’ capability to manage complexity at component assembly lines
-
Enables supplier to work on fast turnaround times from automotive manufacturers
-
Promotes standardisation of quality checks – e.g. displays for quality check images and instructions in the inspection area
-
Allows access to real-time production data
-
Organises and executes assembly from start to finish – from receiving of assembly instructions and sequencing data, to managing the scheduling, assembly, packaging and delivery
-
Integrates scanning and packaging modules to manage packing and delivery in sequence and to correct slots
-
Includes customised barcodes, labels and packaging sheets to manufacturer’s specific needs
-
Supports the management of Bill of Materials
-
Provides production reports for the shopfloor and the back-office
-
Allows assembly line to run independently – in case of a problem in ERP or other company business systems
-
Self-billing option available for high volume component manufacture – automating data transfer helps to avoid mistakes and saves time
Demand flow, or Just-in-Sequence (JIS) manufacturing, is the next step forward from Just-in-Time manufacturing. JIS makes manufacturing processes leaner and helps to cut costs. For example, Automotive Manufacturers can reduce inventories by streamlining production processes and outsourcing component assemblies.
For over a decade Infinity’s sequence production solutions have helped UK Automotive Manufacturers to outsource component assembly and gain competitive advantage. Infinity’s sequence production solutions have helped Automotive Suppliers to set a standard for JIS production and helped to rebuild and strengthen the UK suppliers and supply chains. This has created a benchmark that other manufacturers aspire to achieve.
Infinity’s solutions for suppliers handle real-time data from automotive manufacturers’ and suppliers’ production lines to run Just-in-Time and Just-in-Sequence production. Our system at the supplier’s plant processes and verifies all signals received through Electronic Data Interchange (EDI) connections with the manufacturer’s system. Then the system provides client-specific production instructions, typically involving barcodes/labels and direct IP feeds to production line machinery.
The JIS system at the supplier’s production plant runs production on a daily basis and allows planning ahead of the weekly production schedule. As a web-based application it provides real-time on-demand information. This enables suppliers to react instantly to any fluctuations in actual production levels at the automotive manufacturer’s plant. Supplier can then produce and deliver the right part, at the right time, to the right point in the manufacturing process.

JIT Solutions in a nutshell
-
Bespoke design allows integration with existing production line machines and company ERP software
-
Fully adaptable to manufacturers’ varying production scenarios, volumes and plant sizes
-
Flexible solution for driving continuous improvement – Infinity’s JIT and JIS systems are designed to make process updates and addition of features simple and affordable
-
Improves suppliers responsiveness – receives assembly line status information in real-time from automotive manufacturer’s plants
-
Infinity’s project managers support integration of new suppliers with the automotive manufacturers, as well as the “from scratch” set up of the supplier assembly line
-
Infinity’s experienced engineers manage and carry out the system migration phase
-
24/7 technical support service available – immediate response to issues and queries